Food Manufacturer – Cornwall UK
CASE STUDY – DAIRY CREST
SPECIALIST PIPEWORK FOR A NEW £65 MILLION CREAMERY PROCESS
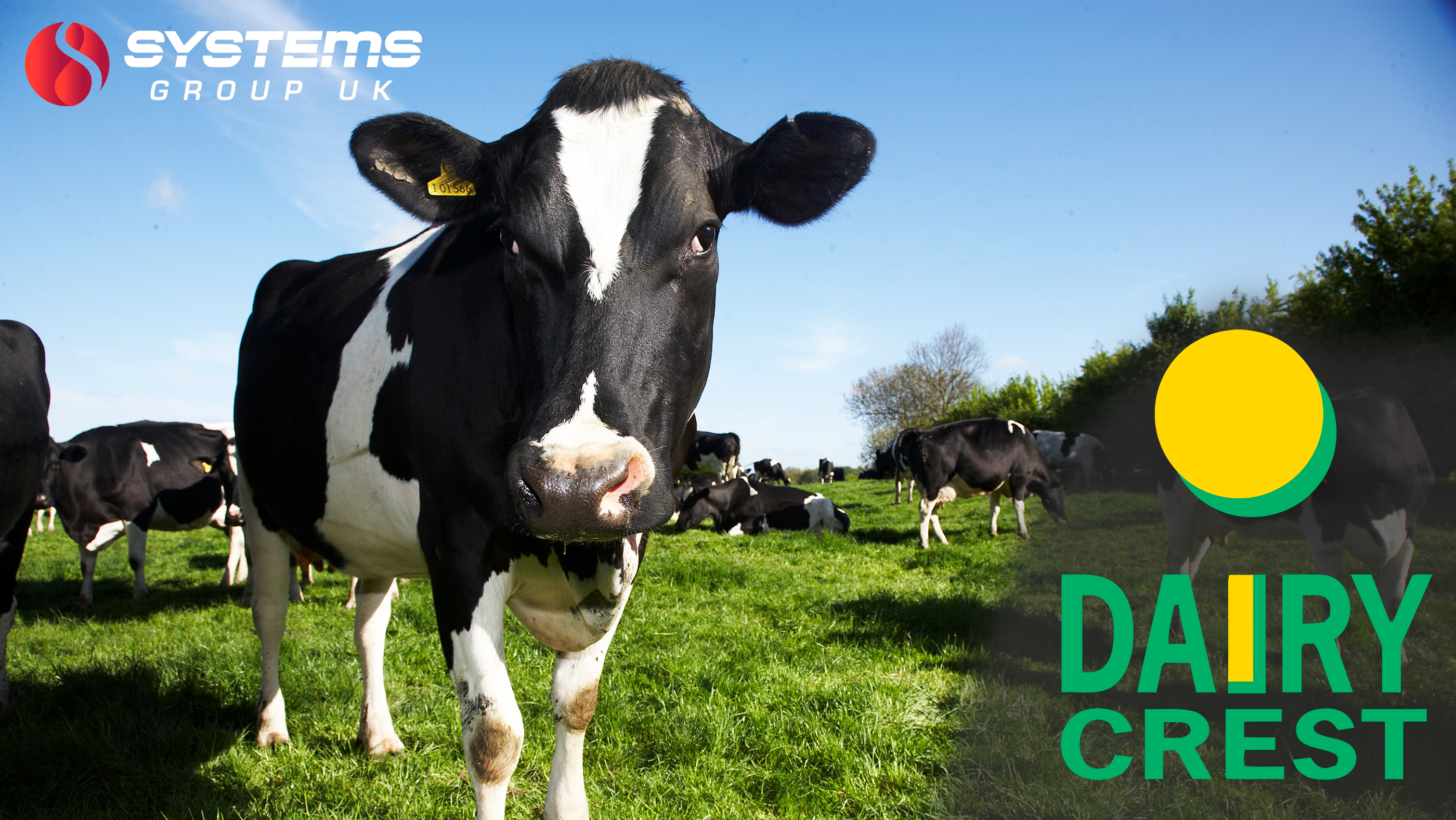
PROJECT DETAIL
Overview
DairyCrest have invested £45 million to manufacture demineralised whey powder for the fast growing global infant formula market. This base ingredient will be produced from the whey generated at its cheese making factory at Davidstow in Cornwall.
The company have also invested £20 million capital at its Davidstow site to manufacture galacto-oligosaccharide (GOS).
GOS is a lactose-based prebiotic, widely used in infant formula.
The new plant processes and demineralises waste cheese by-products which would normally be used as an additive to animal feed to a standard suitable for human consumption (later to be used as a basis for baby milk/powder).
Systems Group successfully tendered and designed, installed and commissioned a host of specialist pipework and fabrications as part of the new facilities.
Cooling Water Pipework
Systems were required to design and install 300mm Sch40 316L stainless steel cooling water pipework running from an energy centre plant room which contained pump stations and roof cooling towers.
The pipework was run high level through a DEMIN cheese store building then at high level onto an external pipe bridge. From there the pipework was run into a DEMIN tank farm and onto a new GOS building which was terminated onto four process plant connections with a suitable valve arrangement.
Chilled Water Pipework
200mm sch40 316L stainless steel chilled water pipework was installed from the energy centre plantroom where pumping stations and internal ammonia chillers are located. Pipework was run high level into the DEMIN process roof void where valve arrangements are located, then connected onto low level process plant within the DEMIN process hall.
Steam and Condensate Mains Pipework
250mm sch40 carbon steel steam pipework and 80mm sch40 316L stainless steel condensate pipework was run at high level through the DEMIN process, through the cheese store, onto the external pipe bridge then into the tank farm and finally terminated within the GOS plantroom.
Steam and Condensate to DEMIN Process
125mm sch40 carbon steel steam pipework and 80mm sch40 316L stainless steel condensate pipework was branched off the steam and condensate mains pipework feeding three pressure reducing stations located on the DEMIN process plant deck. PRV 1 increased steam pipework to 200mm which ran at high level feeding process plant within the DEMIN process hall. All condensates pumped back via spirax sarco high pressure steam pumping stations.
PRV 2 & 3 feeding air handling units located on the demin process plant deck. All AHU condensates were gravity feed to a Spirax Sarco electronic pumping station.
Steam and Condensate to DEMIM Tank Farm
25mm sch40 carbon steel pipework and 20mm sch40 316L stainless steel pipework was branched off mains pipework feeding four spirax sarco pressure reducing stations located on tank farm external plant deck. PRV 3 & 4 feeding air handling units. PRV 5 & 6 running high level into tank farm feeding filtered air units. All condensate pipework was gravity feed back to the mains.
100mm sch40 carbon steel steam pipework and 80mm sch40 316L stainless steel condensate pipework was run feeding a Spirax Sarco pressure reducing station which was externally feeding process water heat exchangers located at low level within the tank farm process area.
RESULT
Additional work requested by client
The client was delighted with the work completed resulting in Systems being requested to take on works outside of the original contract scope. This was due to poor workmanship & quality of installation quality previously provided by another pipework contractor.
The new work completed included; Sch10 316L stainless steel Caustic Acid & Hydrochloric Acid pipework, Hygienic 316L stainless steel thin wall process pipework, plus fabrication and installation of 316 stainless steel framework, pump brackets and pipework supports.
The new dimineralised whey plant is now fully commissioned and operational with the capacity to process 80 tonnes of Dimineralised whey powder per day.
The new GOS plant is now also fully commissioned and operational and has capacity to expand to 35k tonnes of infant formula GOS syrup per annum.
The total project was completed successfully in line with the client specification and timescales.